
Low cost doesn’t normally go hand in hand with high quality. Upholding a reputation for reliability isn’t necessarily compatible with offering a wide range of products. What if it intends to offer a wide range of products? To make things even more complicated, all these decisions involve trade-offs.

Does the company intend to be a low-cost producer and to compete on the basis of price? Or does it plan to focus on quality and go after the high end of the market? Perhaps it wants to build a reputation for reliability. Before making decisions about the operations process, managers must consider the goals set by marketing managers. The decisions made in the planning stage have long-range implications and are crucial to a firm’s success. Let’s take a closer look at each of these responsibilities. Finally, the operations manager is directly involved in efforts to ensure that goods are produced according to specifications and that quality standards are maintained. At this stage, they also oversee the purchasing of raw materials and the handling of inventories. They must solicit and respond to feedback and make adjustments where needed. Once the production process is under way, managers must continually schedule and monitor the activities that make up that process. During production planning, managers determine how goods will be produced, where production will take place, and how manufacturing facilities will be laid out. That person’s responsibilities can be grouped as follows: Making the decisions involved in the effort to attain these goals is the job of the operations manager. They must fine-tune their production processes to focus on quality, to hold down the costs of materials and labor, and to eliminate all costs that add no value to the finished product. To perform this function in today’s business environment, manufacturers must continually strive to improve operational efficiency. Like PowerSki, all manufacturers set out to perform the same basic function: to transform resources into finished goods. Figure 11.1 “The Transformation Process” illustrates this traditional function of operations management. In other words, operations managers manage the process that transforms inputs into outputs. The job of operations management (OM), then, consists of all the activities involved in transforming a product idea into a finished product, as well as those involved in planning and controlling the systems that produce goods and services.

The upper-level manager who directs this transformation process is called an operations manager.
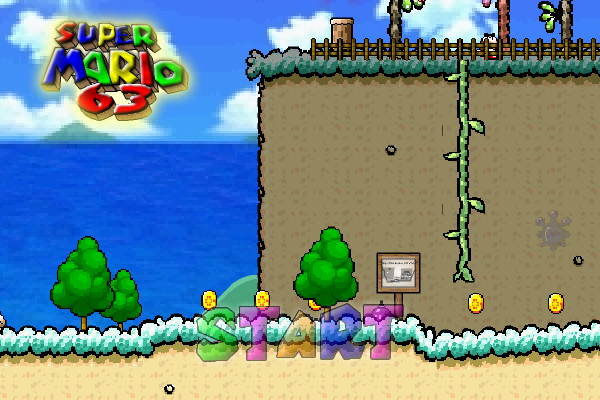
Thus, to compete with other organizations, a company must convert resources (materials, labor, money, information) into goods or services as efficiently as possible. Like PowerSki, every organization-whether it produces goods or provides services-sees Job 1 as furnishing customers with quality products. Describe the decisions made in planning the production process in a manufacturing company.Define operations management, and discuss the role of the operations manager in a manufacturing company.
